Nimonic Alloys: The High-Temperature, Low Creep Superalloys
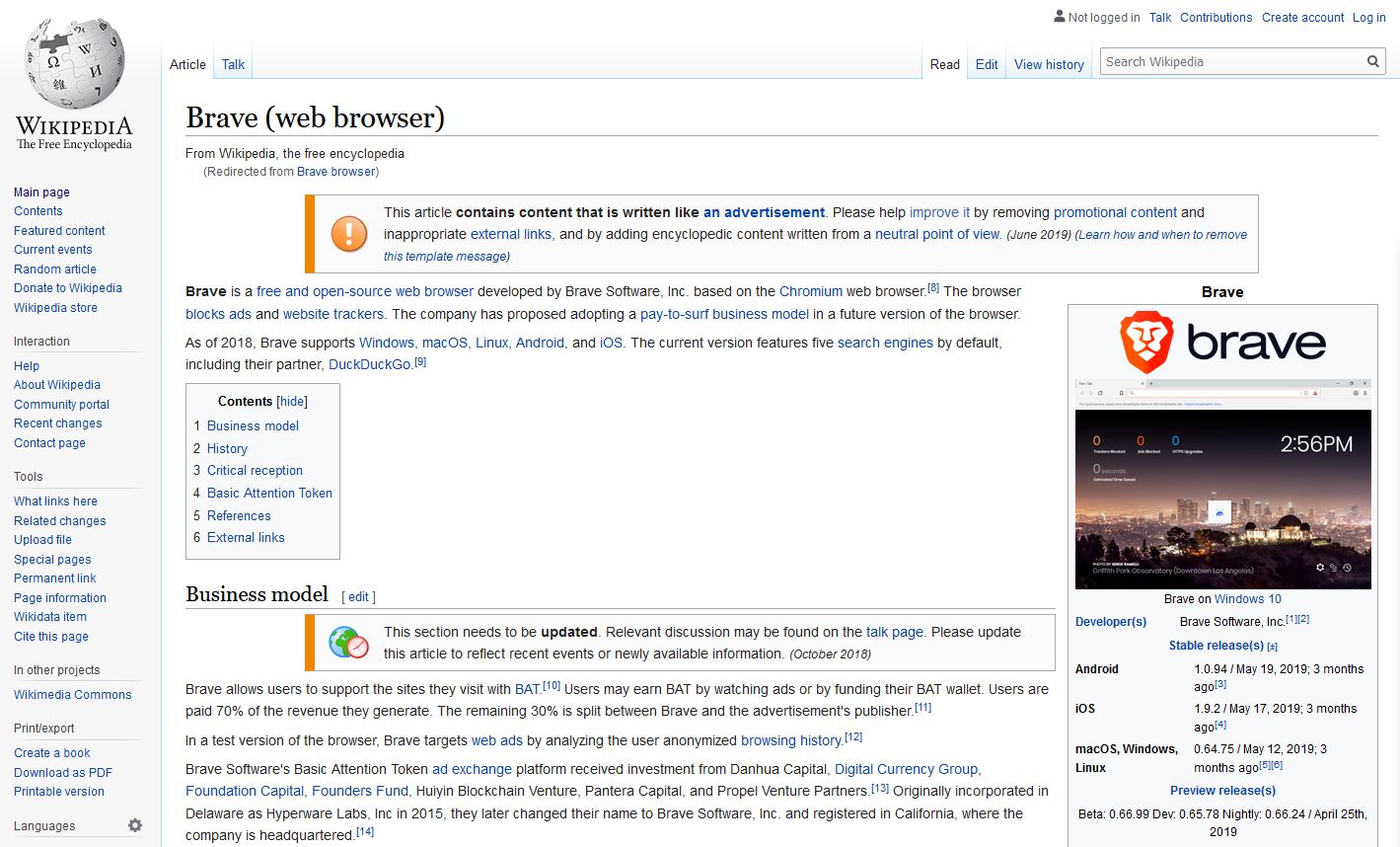
From powering a gas turbine to driving a reciprocating engine, engineering materials that can withstand high temperatures, stress, and corrosion is a mammoth task. It is here that the family of nickel-based Nimonic alloys comes into play. Known for their remarkable high-temperature strength, low creep, and excellent corrosion resistance, Nimonic alloys have become the material of choice for a range of critical applications in the aerospace, power generation, and chemical processing industries.
A Brief History of Nimonic Alloys
Developed in the 1940s by research teams at the Wiggin Works in Hereford, England, Nimonic alloys were originally conceived in support of the Whittle jet engine project. The project aimed at building a reliable jet engine that could power military aircraft. The high-temperature strength requirements of the engine necessitated the development of a new class of alloys.
Nimonic alloys are nickel-based alloys that contain up to 20% chromium, and other elements such as titanium, aluminum, and cobalt. The alloys are characterized by their remarkable strength at high temperatures, low creep, and excellent corrosion resistance properties. These properties make them ideal materials for applications that require high-temperature stability and resistance to stress-corrosion cracking.
Applications of Nimonic Alloys
The unique properties of Nimonic alloys make them suitable for a range of critical applications across several industries. Some common applications of Nimonic alloys are:
1. Gas Turbines: Gas turbines are used in a range of applications including power generation, aviation, and marine propulsion. Nimonic alloys are used primarily in the hot end of gas turbines, where temperatures can reach as high as 1100 degrees Celsius.
2. Reciprocating Engines: Reciprocating engines are used in a wide range of applications including power generation, transport, and heavy machinery. Nimonic alloys are used in the pistons, valves, and exhaust systems of these engines owing to their high-temperature strength, low creep, and corrosion resistance.
3. Aerospace: The aerospace industry relies heavily on Nimonic alloys owing to their ability to withstand the high-stress environment of space travel. Nimonic alloys are used in a range of aerospace applications including turbine blades, exhaust systems, and high-temperature fasteners.
4. Chemical Processing: The corrosive environment of chemical processing requires materials that can withstand the aggressive chemicals and high temperatures encountered in these processes. Nimonic alloys are used in heat exchangers, reaction vessels, and pumps in chemical processing plants.
Advantages of Nimonic Alloys
1. High-Temperature Strength: Nimonic alloys retain their strength even at high temperatures, making them ideal for use in hot end applications such as gas turbines.
2. Low Creep: The low creep properties of Nimonic alloys make them suitable for use in applications where minimal deformation is required.
3. Corrosion Resistance: Nimonic alloys exhibit excellent corrosion resistance properties, making them ideal for use in harsh environments such as chemical processing plants.
4. Stress Corrosion Cracking Resistance: Nimonic alloys are highly resistant to stress corrosion cracking, making them ideal for use in high-stress environments.
5. Research and Development: The ongoing research and development in Nimonic alloys have led to the introduction of new alloys with even better properties, making them ideal for use in a range of critical applications.
Conclusion
Nimonic alloys have become the material of choice for a range of critical applications across several industries. The unique properties of Nimonic alloys, such as high-temperature strength, low creep, and excellent corrosion resistance, make them ideal for use in applications that require materials that can withstand the harsh environment of high-temperature and stress environments. As research and development continue in this field, the use of Nimonic alloys is expected to increase in a range of critical applications in the future.